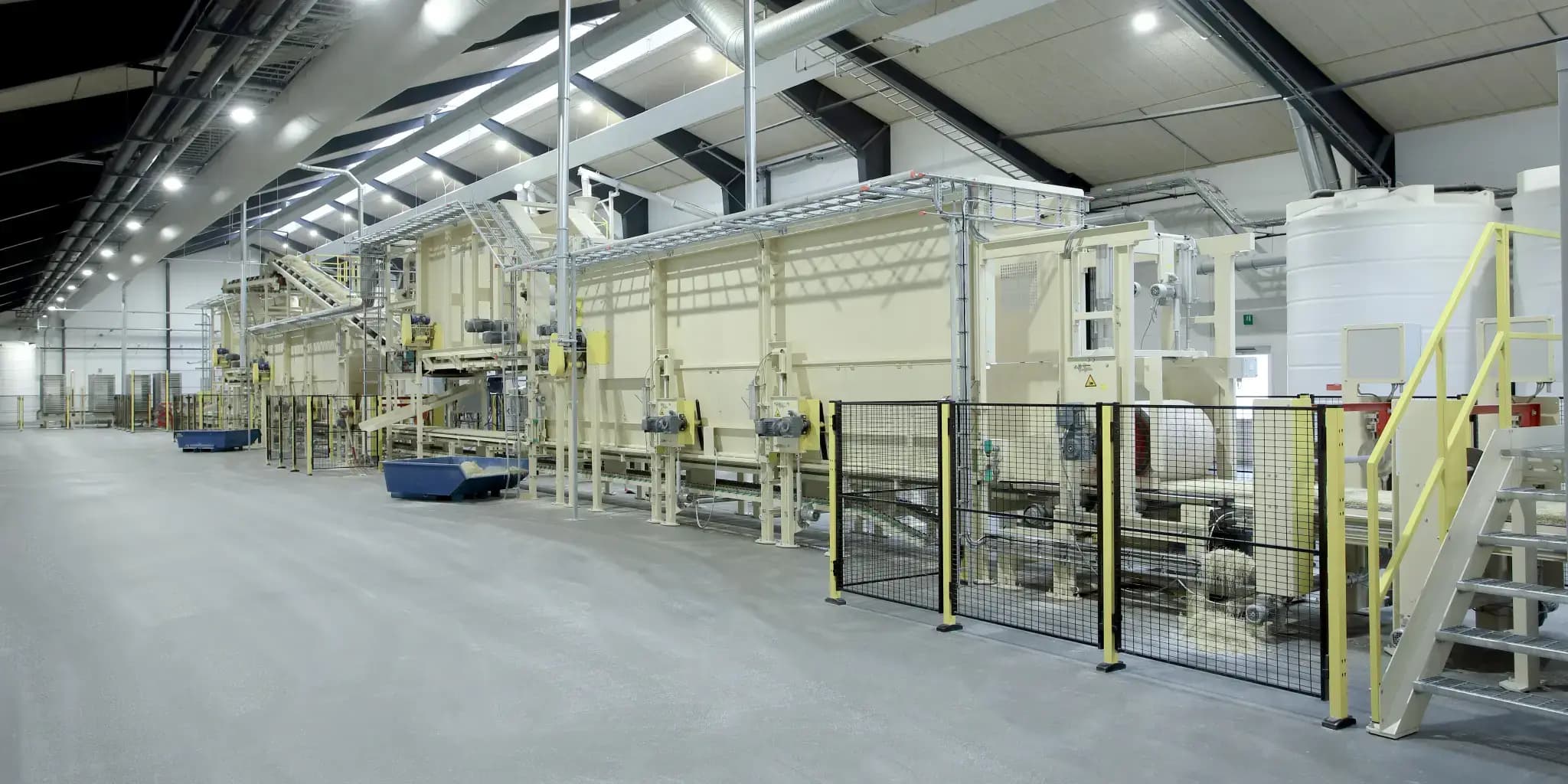
Wood Wool Cement Board Plant
Wood Wool Cement Board (WWCB) production lines
An Eltomation WWCB plant is a fully automated production facility designed with efficiency, consistency, and sustainability in mind. The process begins with producing wood wool, which is then mixed with cement and water to form durable, high-performance boards. These versatile boards offer excellent acoustic, thermal, and structural properties, making them ideal for various applications in modern design and construction.
Rooted in Wood Wool Cement Boards
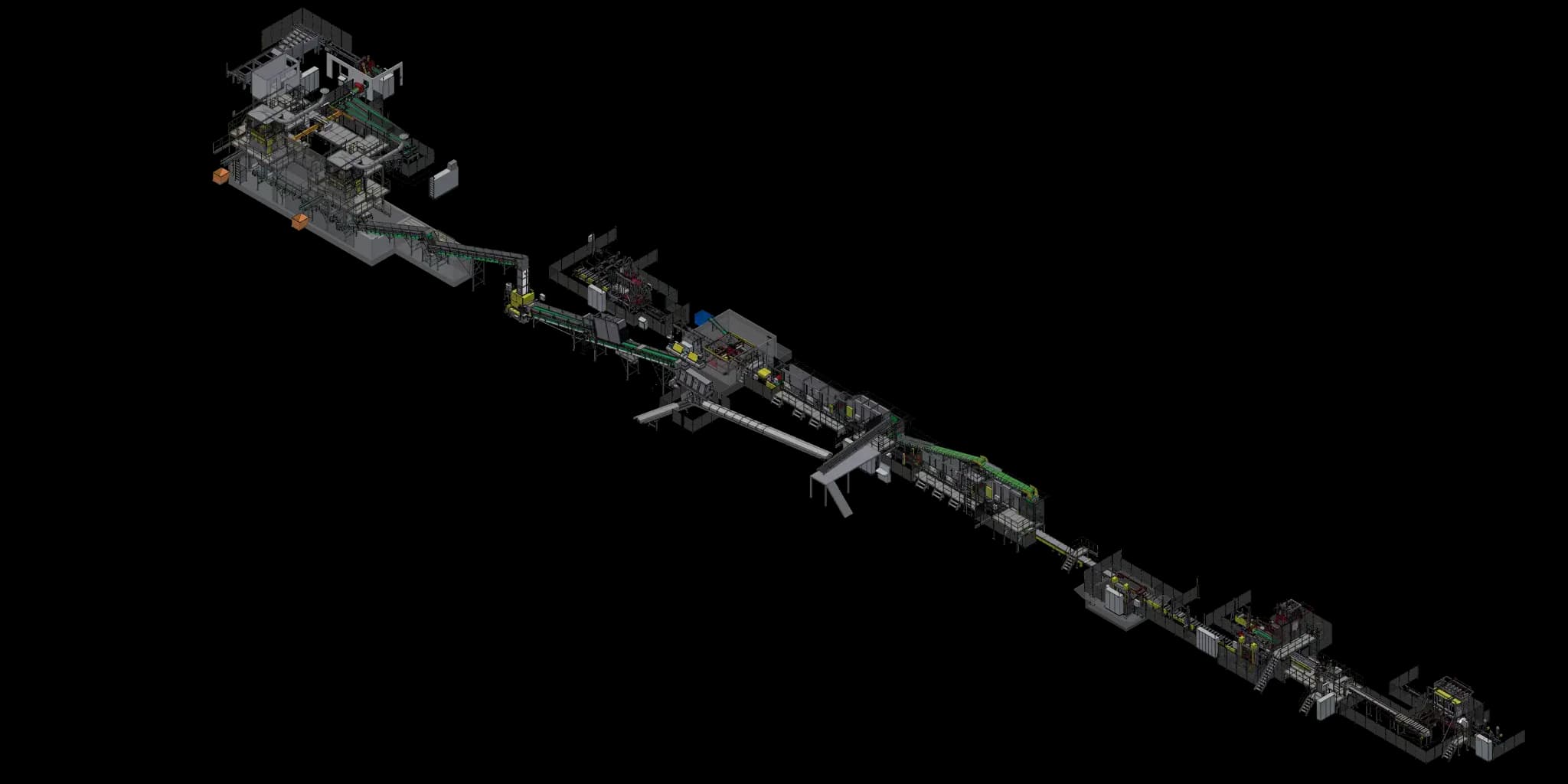
Key WWCB plant characteristics
- capacity of up to 4.300 m2 per shift (25 mm board)
- plant size: approx. 210 x 84 m (three shifts)
- line speed of 20,9 m/min.
- board dimensions: 2000/2400 x 600 mm
- board thickness: 15 to 35 mm for acoustic boards
- board thickness: up to 150 mm for insulation boards
- board thickness: up to 100 mm for construction boards
- wood wool width: 1 / 1.5 / 2 / 3 mm
- only 4 operators required on the Eltomation line
Contact us for a budget quote
FAQ
What are the electric power requirements to operate a WWCB plant?
For the Eltomation production line alone, the estimated installed capacity is approx. 900 kVA. When adding finishing operations, total installed power requirements are estimated at 1800 kVA.
How can you promote sustainable products if cement is used in the recipe?
While cement production contributes to CO₂ emissions, the industry is actively working on solutions to reduce its impact. In WWCB production, more than half of the board’s mass consists of renewable wood and water, making it a more sustainable option than many traditional building materials. Additionally, the low density of WWCB means that less material is needed to cover a given volume, further improving its environmental footprint. In general, we can state that 1 m³ of wood used creates approx. 4 m³ of end product.
Our plants are designed to (optionally) use LC3 cement as a lower-carbon alternative to standard Portland cement without compromising board quality. In addition, many of our clients add a percentage of limestone to reduce the overall cement content, further lowering emissions while maintaining durability and performance.
What are the raw material needed to produce boards or wall elements?
For all products coming from the production lines the ingredients are the same: softwood (typically pine or spruce), cement and water. Additives like limestone can be added to the mix to reduce the cement content and tweak the product for certain use cases. Rough proportions of the raw materials are as follows:
Wood wool: 31%
Cement: 45%
Water: 22%
Waterglass: 2%
Are your plants geared for circular manufacturing?
Our large element line runs a zero-waste production process, with all trimming waste reintegrated into new products. For our standard lines, we are actively working on recycling all trimming waste back into production. However, we do not process construction waste from demolition sites.
Can wall elements and acoustic panels be made on the same production line?
No. Only the very first section of the production line (block handling, production of wood wool and mixing with water and cement) is the same. After the dosing and mixing process, the production lines for acoustic panels and large elements follow the same principle but are created on different machines.
Does Eltomation also provide support during construction and land preparation for a new facility?
We have extensive knowledge we can share when it comes to raw materials needed, log yard capacity, dust extaction capacity, etc. we share in detail in the pre-engineering stage once we seriously proceed with a project.
How many plants have you supplied?
The company’s origins are in the 1950s. Since then, over 130 projects have been realized.
How much time is required to switch to another product type?
Switching between product thicknesses (using the same wood wool type) takes only a few minutes. A new form is supplied to the line, and settings adjust automatically in the Control System. Changing wood wool types (e.g., from 1.0 mm to 2.0 mm) requires swapping the 16 pre-assembled knife cassettes in the Eltomatic, which takes about 15 minutes – typically done during a break.
How many shifts per day are WWCB lines operational?
Operational requirements vary per client. WWCB plants are designed for full 2- or 3-shift production, with each shift running for 7 hours plus 1 hour for cleaning. Most lines operate 5-6 days per week.
Do you also provide technical assistance in the ramp up phase?
Yes. Several Eltomation personnel will remain on site for 6 weeks after first commissioning to make sure the plant runs smoothly, and local operators / supervisors are properly trained.
Have other questions?
We would love to get in touch to discuss your needs.
Reach out to us today!