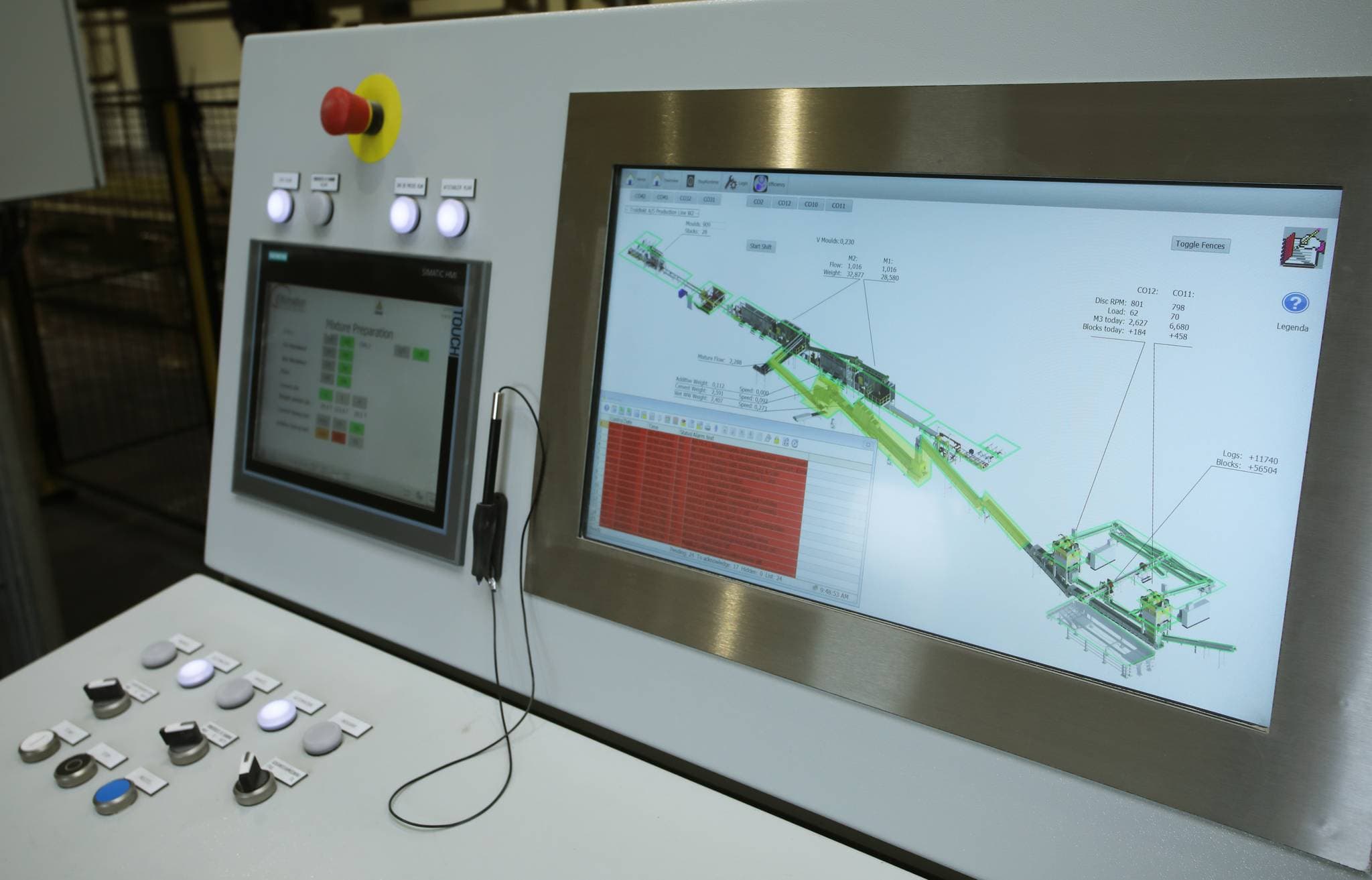
Insulation Board Line
Produce Composite WWCB boards with an insulation core
The Eltomation WWCB plant can be equipped with a robotic core insert system, enabling the automated production of so-called 2- or 3- layer composite WWCB boards. These board provide for a further increased thermal insulation and fire-resilience, as may be required in parking houses, fire-escapes, etc.
An AGV transport system ensures safe and efficient movement of stacks throughout the facility. Notably, the same plant can also produce acoustic panels, allowing production to easily switch between standard WWCB boards and composite boards between shifts.
Rooted in Insulation Boards
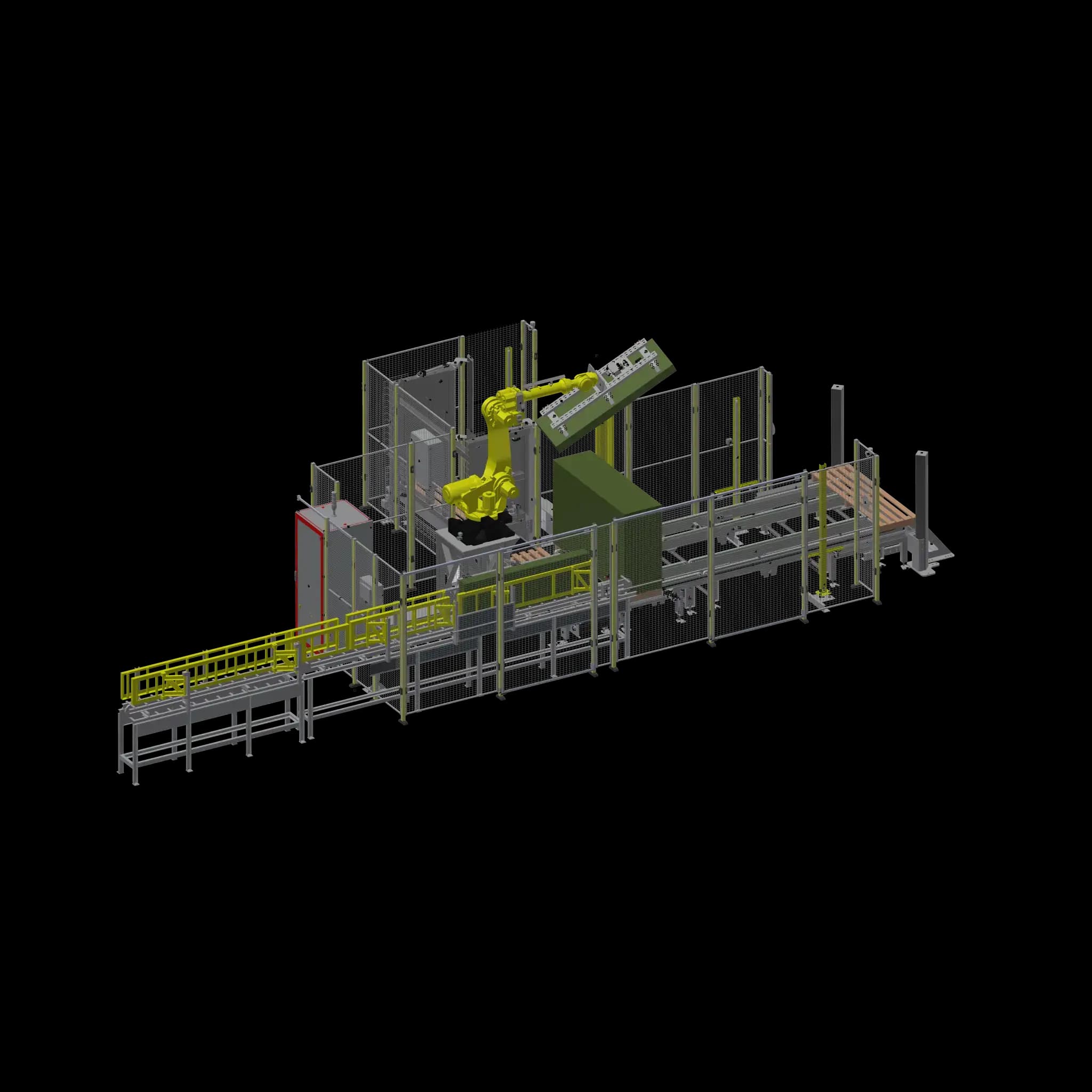
Key notes on the production line
-
produce 2-layer or 3-layer insulation boards
-
cores up to 150 mm (6”) can be handled in the line
-
capacity of 2800 boards per shift (2000 x 600 mm)
-
typical WWCB layer(s) 5, 10, 15 mm (3/16”, 3/8”, 5/8”)
-
increased safety with the use of AGVs
-
easily switch between production output
High-Performance Insulation with WWCB
Insulation boards featuring a layer of Wood Wool Cement Board (WWCB) provide exceptional thermal performance, making them an excellent choice for a wide range of construction applications. These boards are particularly well-suited for parking houses, where they help regulate temperature while also offering durability and resistance to environmental conditions.
In addition to their use in roof and floor insulation for passive housing, WWCB insulation boards play a crucial role in enhancing energy efficiency, contributing to reduced heating and cooling costs. Their high fire resilience makes them an ideal solution for fire-rated walls, ceilings, and parking deck ceilings, ensuring compliance with stringent safety regulations while providing long-lasting protection.
Furthermore, these boards offer superior sound absorption, reducing noise transmission and enhancing acoustic comfort in buildings. This makes them particularly valuable for applications in residential, commercial, and industrial settings, where both thermal insulation and noise reduction are key factors in improving indoor living and working environments.
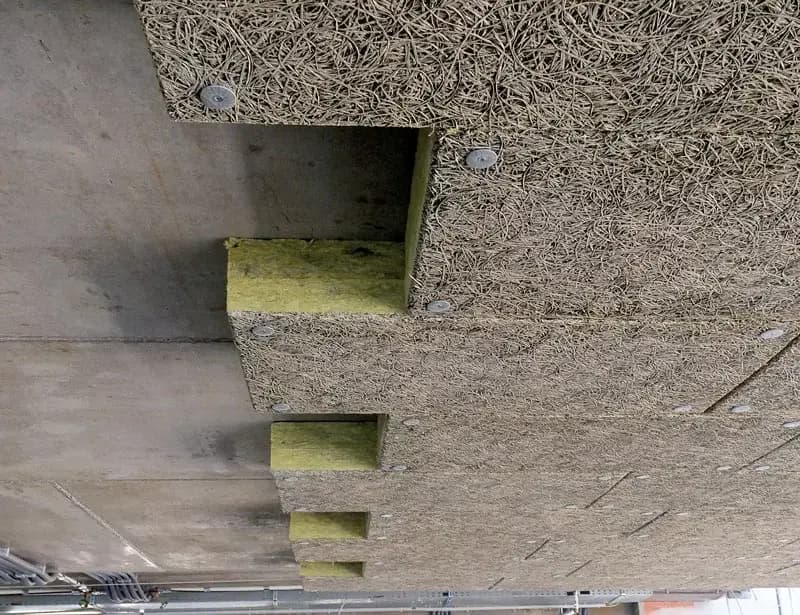
FAQ Composite Insulation Boards
Are WWCB insulation boards easy to install?
Yes, the boards are lightweight and can be installed using standard construction methods. They are often mounted with special screws, and their flexible nature allows them to be cut and shaped easily on-site. Get in contact with us to learn more.
Can WWCB insulation boards be used in humid environments?
Yes, due to their cement content, WWCB boards have excellent moisture resistance. They can be used in environments with high humidity, such as basements, swimming pools, or cold storage facilities, without deteriorating.
Are WWCB insulation boards effective for sound absorption?
Yes, the porous structure of wood wool, combined with insulation materials like mineral wool, offers high sound absorption performance. This makes these boards ideal for applications where noise reduction is important, such as in acoustic panels and ceilings.
How do these boards perform in terms of fire resistance?
WWCBs are inherently fire-resistant, achieving classifications such as B-s1,d0 and A2-s1,d0 (non-combustible) according to EN standards. The inclusion of mineral wool, EPS or XPS cores enhances this fire resistance, providing added safety in building constructions.
What is the maximum thickness of insulation material that can be processed on an Eltomation line?
Our lines can handle boards with a total thickness of up to 150 mm (6”).
What insulation materials can be handled on an Eltomation line?
Eltomation lines are designed to handle most common insulation materials, provided they are stiff. Core sheets typically consist of mineral wool, EPS or XPS (subject to applications) to which a one- or two-sided thin layer of WWCB is added. Contact us if you would like to process other materials.
What are the electric power requirements to operate a WWCB plant?
For the Eltomation production line alone, the estimated installed capacity is approx. 900 kVA. When adding finishing operations, total installed power requirements are estimated at 1800 kVA.
Do you also provide technical assistance in the ramp up phase?
Yes. Several Eltomation personnel will remain on site for 6 weeks after first commissioning to make sure the plant runs smoothly, and local operators / supervisors are properly trained.
Have other questions?
We would love to get in touch to discuss your needs.
Reach out to us today!