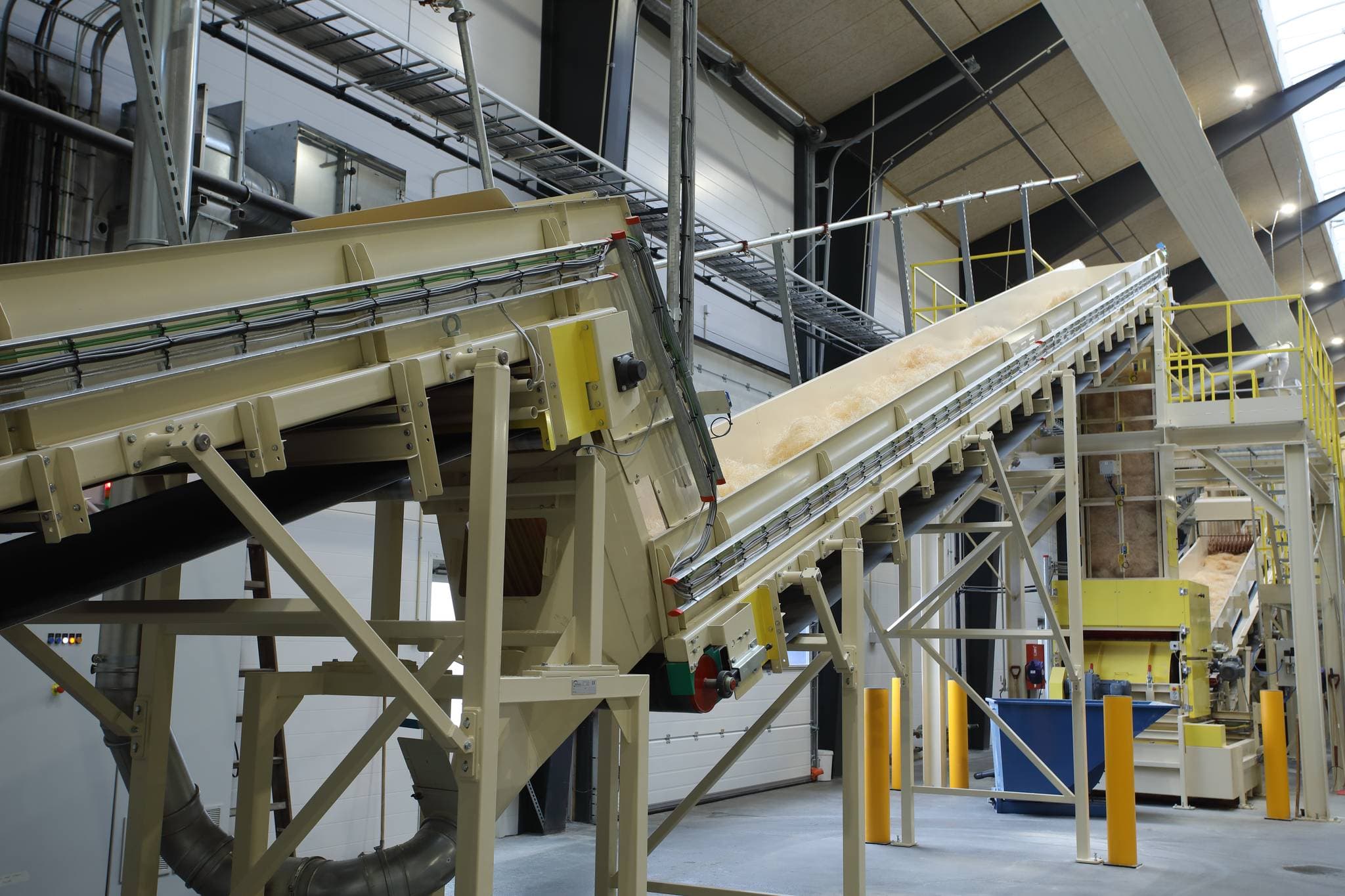
Production lines
Our advanced production lines
Eltomation line key features
Excellence in every detail – what you can expect from our production lines:
-
Full automation – Ensuring efficiency, precision, and reduced labor costs.
-
High output – Optimized processes for large-scale production.
-
Flexibility – Easily switch between board types or production configurations.
-
Sustainability – Minimal waste, energy-efficient designs, and eco-friendly materials.
-
Advanced technology – Featuring robotic handling, AGVs, and precision control systems.
General product properties
Our production lines ensure you produce high-quality boards, built to perform:
- Excellent acoustic & thermal properties – Ideal for energy-efficient and sound-absorbing solutions.
- Fire resistance – Meeting strict safety standards for various applications.
- Durability – Robust and long-lasting, ensuring reliable performance over decades.
- 100% natural composition – Sustainable, emission-free, and recyclable.
- Customizable options – Tailored dimensions, densities, and finishes to meet market demands.
Recent resources
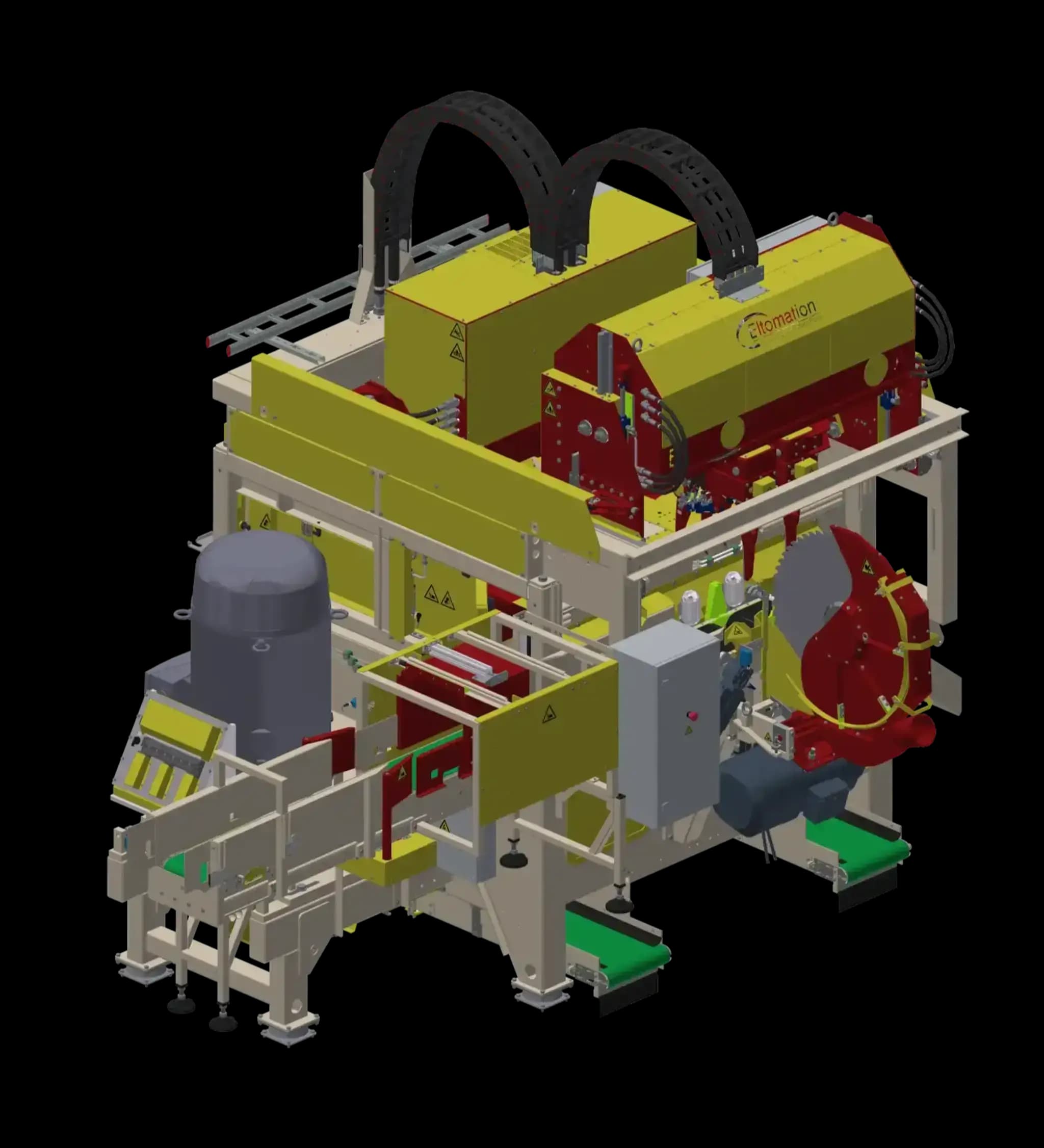
The Eltomatic Wood Wool Machine
In a world increasingly embracing eco-friendly solutions, the Eltomatic Fully Automated Wood Wool Machine sets a new standard for wood wool production. Designed to deliver high-quality wood wool with exceptional consistency and capacity, the Eltomatic serves as the core of modern Wood Wool Cement Board (WWCB) plants and facilities producing biodegradable products for packaging and erosion control. With its versatility, safety features, and state-of-the-art automation, this machine is the ultimate solution for industries seeking sustainable materials and efficient operations.
FAQ
How many plants have you supplied?
The company’s origins are in the 1950s. Since then, over 130 projects have been realized.
Do you only deliver greenfield projects?
No. Most of our customers already have a facility and would like to repurpose that facility with an Eltomation production line. Together with the customer we review all layout options to come to the most optimal solution.
What is a typical facility size?
210 x 85 m would be the typical size of a WWCB plant operating three shifts a day with a wood yard of 1 to 1.5 ha.
320 x 80 m would be the typical floor space for a large element production plant.
50 x 30 m would be the typical size for a wood wool production plant.
Are your plants geared for circular manufacturing?
Our large element line runs a zero-waste production process, with all trimming waste reintegrated into new products. For our standard lines, we are actively working on recycling all trimming waste back into production. However, we do not process construction waste from demolition sites.
What are the raw material needed to produce boards or wall elements?
For all products coming from the production lines the ingredients are the same: softwood (typically pine or spruce), cement and water. Additives like limestone can be added to the mix to reduce the cement content and tweak the product for certain use cases. Rough proportions of the raw materials are as follows:
Wood wool: 31%
Cement: 45%
Water: 22%
Waterglass: 2%
Can wall elements and acoustic panels be made on the same production line?
No. Only the very first section of the production line (block handling, production of wood wool and mixing with water and cement) is the same. After the dosing and mixing process, the production lines for acoustic panels and large elements follow the same principle but are created on different machines.
Do you also deliver turn-key solutions for cement-bonded particle board (CBPB) production?
No, we don’t. For those who are interested in cement-bonded high-density boards we offer the EltoBoard press as an extension to a regular WWCB plant. More information can be found here.
What information do you need to design a plant for us?
To design a plant for you, we need indication on the product range you wish to produce and whether the lines need to run 1, 2 or up to 3 shifts per day. In addition, we need key details about the planned location—whether it's a greenfield site or an existing facility. For installation within an existing building, a detailed CAD drawing is essential, including height and column spacing. Additionally, we require insight into the surrounding area to ensure proper access roads and space for silos in the case of a WWCB plant.
Does Eltomation also provide support during construction and land preparation for a new facility?
We have extensive knowledge we can share when it comes to raw materials needed, log yard capacity, dust extaction capacity, etc. we share in detail in the pre-engineering stage once we seriously proceed with a project.
How much time is required to switch to another product type?
Switching between product thicknesses (using the same wood wool type) takes only a few minutes. A new form is supplied to the line, and settings adjust automatically in the Control System. Changing wood wool types (e.g., from 1.0 mm to 2.0 mm) requires swapping the 16 pre-assembled knife cassettes in the Eltomatic, which takes about 15 minutes – typically done during a break.
Have other questions?
We would love to get in touch to discuss your needs.
Reach out to us today!