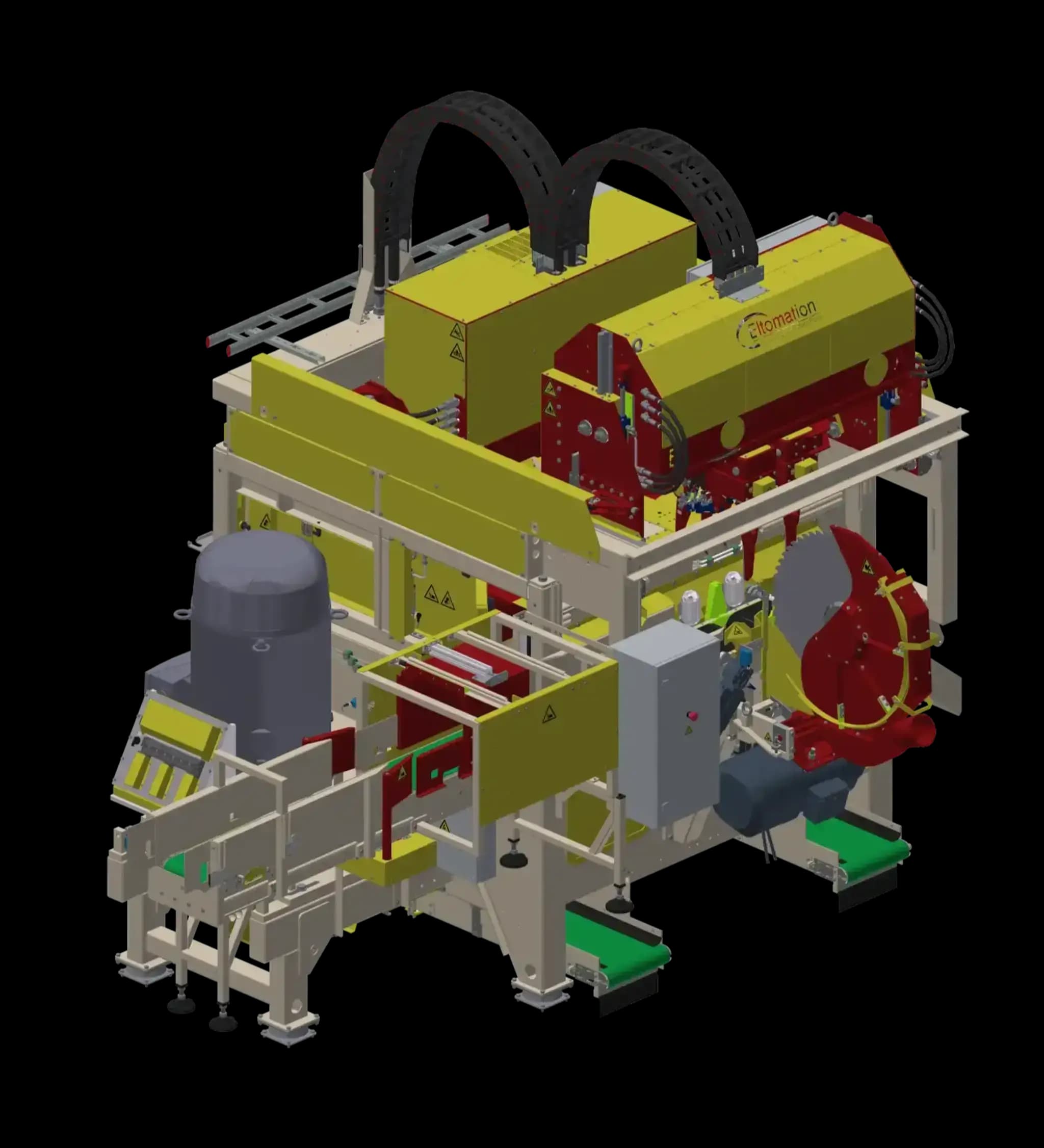
The Eltomatic Wood Wool Machine
In a world increasingly embracing eco-friendly solutions, the Eltomatic Fully Automated Wood Wool Machine sets a new standard for wood wool production. Designed to deliver high-quality wood wool with exceptional consistency and capacity, the Eltomatic serves as the core of modern Wood Wool Cement Board (WWCB) plants and facilities producing biodegradable products for packaging and erosion control. With its versatility, safety features, and state-of-the-art automation, this machine is the ultimate solution for industries seeking sustainable materials and efficient operations.
The Eltomatic Wood Wool Machine
In a world increasingly embracing eco-friendly solutions, the Eltomatic Fully Automated Wood Wool Machine sets a new standard for wood wool production. Designed to deliver high-quality wood wool with exceptional consistency and capacity, the Eltomatic serves as the core of modern Wood Wool Cement Board (WWCB) plants and facilities producing biodegradable products for packaging and erosion control. With its versatility, safety features, and state-of-the-art automation, this machine is the ultimate solution for industries seeking sustainable materials and efficient operations.
Diverse Applications of Wood Wool
Wood wool, also known as excelsior, is a highly versatile material that aligns perfectly with modern sustainability goals. The Eltomatic produces wood wool tailored to a wide range of applications, including:
- Sustainable Building Materials: Our roots lie in creating sustainable building materials by combining wood wool with cement. The thin cement coating enhances resistance to fire, mold, fungi, and water, while the low density structure of cement-bonded wood wool provides excellent sound absorption and insulation. This combination is widely used in acoustic boards for public buildings, schools, and offices. Additionally, large panels made from wood wool cement boards can be utilized in prefab housing solutions.
- Biodegradable Packaging: The natural hygroscopic properties of wood wool make it ideal for packaging items like seafood and fresh produce. It absorbs and releases moisture, cushions fragile goods during transportation, and maintains ventilation to reduce spoilage and mold growth. This makes wood wool a practical and eco-friendly alternative for food packaging.
- Erosion Control: Wood wool is also used in erosion control blankets, where it retains soil moisture, promotes vegetation growth, and reduces wind and water erosion. As it decomposes, wood wool enriches the soil, supporting long-term health and sustainability. This dual-purpose solution provides immediate protection and lasting soil improvement. The growing market demand for high-quality wood wool reflects a global shift toward sustainable, eco-conscious alternatives. The Eltomatic enables industries to meet this demand effectively.
Advancing Beyond Traditional Wood Shaving Machines
While wood wool production has been around for over a century, the Eltomatic brings unparalleled advancements in safety, productivity, and efficiency. Here’s how it compares to traditional wood shaving machines:
- Safety: Fully automated in a safety room, reducing risks
- Productivity: ~2,200 kg/hour, replacing up to 6 machines
- Time between sharpening: Approximately 16 hours
- Efficiency: Operates with only 1 supervisor, even with multiple Eltomatics
- Near-zero waste: 99% block utilization
The Eltomatic's advanced automation includes a block buffer system that ensures a continuous flow of wood blocks and allows for automatic diameter-based mixing before feeding.
Cutting-Edge Automation and Design
The Eltomatic is a fully automated system with servo-driven technology for precise block handling and feeding. It processes debarked wood blocks up to 50 cm (25”) long and 26 cm (12”) in diameter, cutting them into uniform wood wool strands.
At its core, the machine features a rotating disc equipped with 16 quick-change knife sets. Designed specifically by Eltomation, these knives accommodate softwoods like pine, spruce, aspen and poplar. They can produce wood wool in widths from 1 to 3 mm and thicknesses between 0.1 and 0.4 mm, meeting diverse market demands.
Minimal waste is generated during operation, and any cutting dust or residual material is collected for reuse as clean raw material.
Dimensions & Power Requirements
- Length: 6,500 mm
- Width: 5,500 mm
- Installed power: 300 kVA (Average consumption: 180 kW)
- Compressed air: 7 bar at 60 Nm³/hour
- Dust extraction: 10,650 Nm³/hour
Unparalleled Production Capacity
The Eltomatic delivers unmatched output while maintaining precise wood wool quality. Production capacity ranges from 1,000 kg/hour for extremely thin strands to 3,400 kg/hour for thicker ones, depending on block diameter. For applications like eco-friendly packaging requiring 0.15 mm thickness, the machine achieves up to 2,020 kg/hour.
• Block Diameter 265 mm > 3,419 kg/hour
• Block Diameter 220 mm > 2,662 kg/hour
• Block Diameter 200 mm > 2,335 kg/hour
• Block Diameter 150 mm > 1,550 kg/hour
• Block Diameter 130 mm > 1,169 kg/hour
By replacing up to 8 older reciprocating machines, the Eltomatic enhances production efficiency and reduces operational costs significantly.
Full System Integration
Although the Eltomatic can operate as a standalone machine, Eltomation offers fully integrated solutions, including automated log infeed, block cutting systems, and transfer conveyors. The advanced block buffer system ensures uninterrupted production and handles temporary downtimes or maintenance efficiently. For more information on integrated system solutions, visit the Wood Wool Production Plant page.
Operating and Maintaining the Eltomatic
The Eltomatic is designed for simplicity and reliability. A single supervisor can oversee its operation from an HMI display and CCTV in the operations room. Key settings, such as disc RPM and wood wool thickness, can be adjusted remotely. Maintenance is straightforward, with quick-change knife sets that require sharpening after each shift. The machine’s modular design, including a removable top frame, allows easy access for servicing critical components.
Modernizing the Eltomatic
Since its introduction in 2000, over 45 Eltomatic machines have been installed worldwide, many operating up to three shifts per day. Eltomation continually updates its design, incorporating features like improved gripper frames, advanced bearings, and enhanced safety mechanisms. Modular upgrades ensure older models remain efficient and compliant with modern standards. Typical upgrades include a new gripper frame as well as improvements to the pusher and frame positioning where position and speed are adjusted every 10 milliseconds, to ensure smooth, precise movements, even when processing the last piece of each block. Unlike hydraulic systems, performance remains stable and unaffected by oil temperature variations.