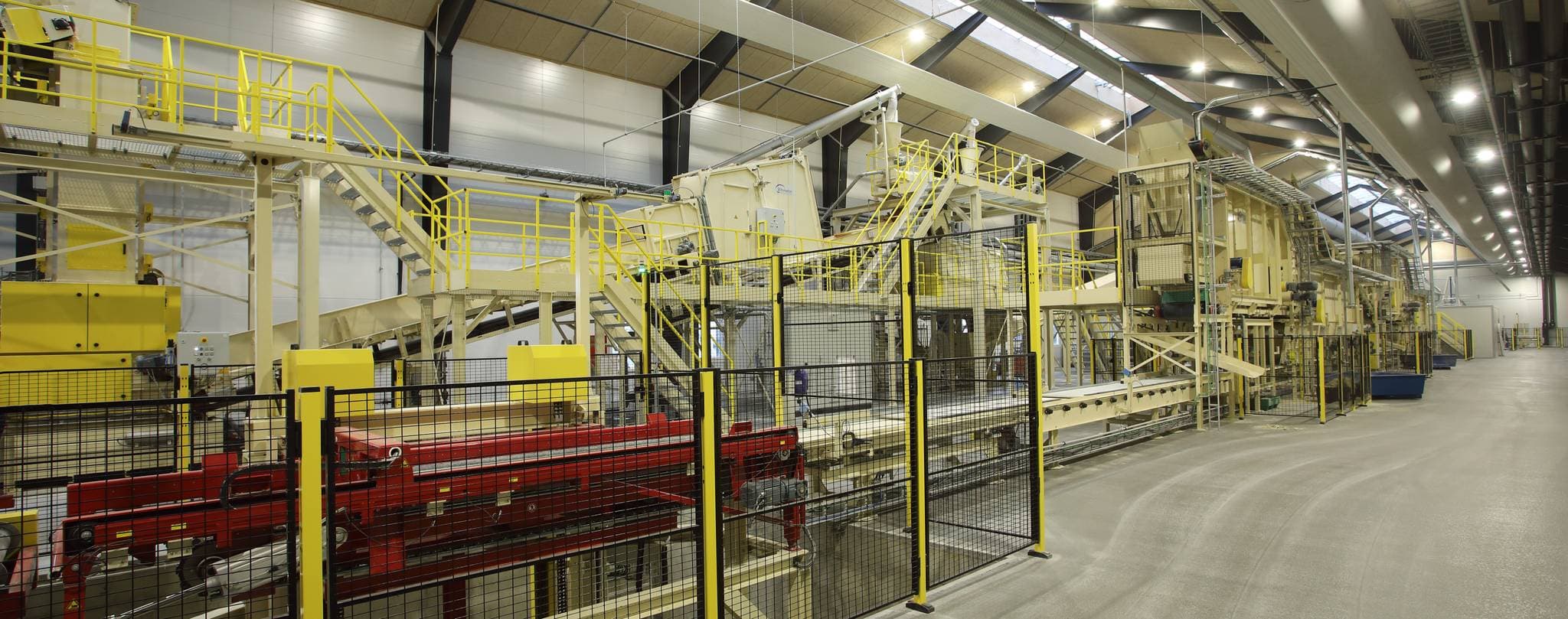
Medium Density EltoBoards
Produce Medium-Density EltoBoards
For medium-density WWCB boards, Eltomation has developed a specialized clamping press that can be added to the end of a standard WWCB production line. This press compresses the boards to a density of approximately 1100 kg/m³ (68 lbs/ft3). The resulting medium-density EltoBoard is commonly used in flooring, permanent shuttering, and SIP panels. Thanks to its non-combustibility, EltoBoard is a safe and effective alternative to OSB and CBPB in projects with stringent fire safety requirements, particularly in high-rise buildings.
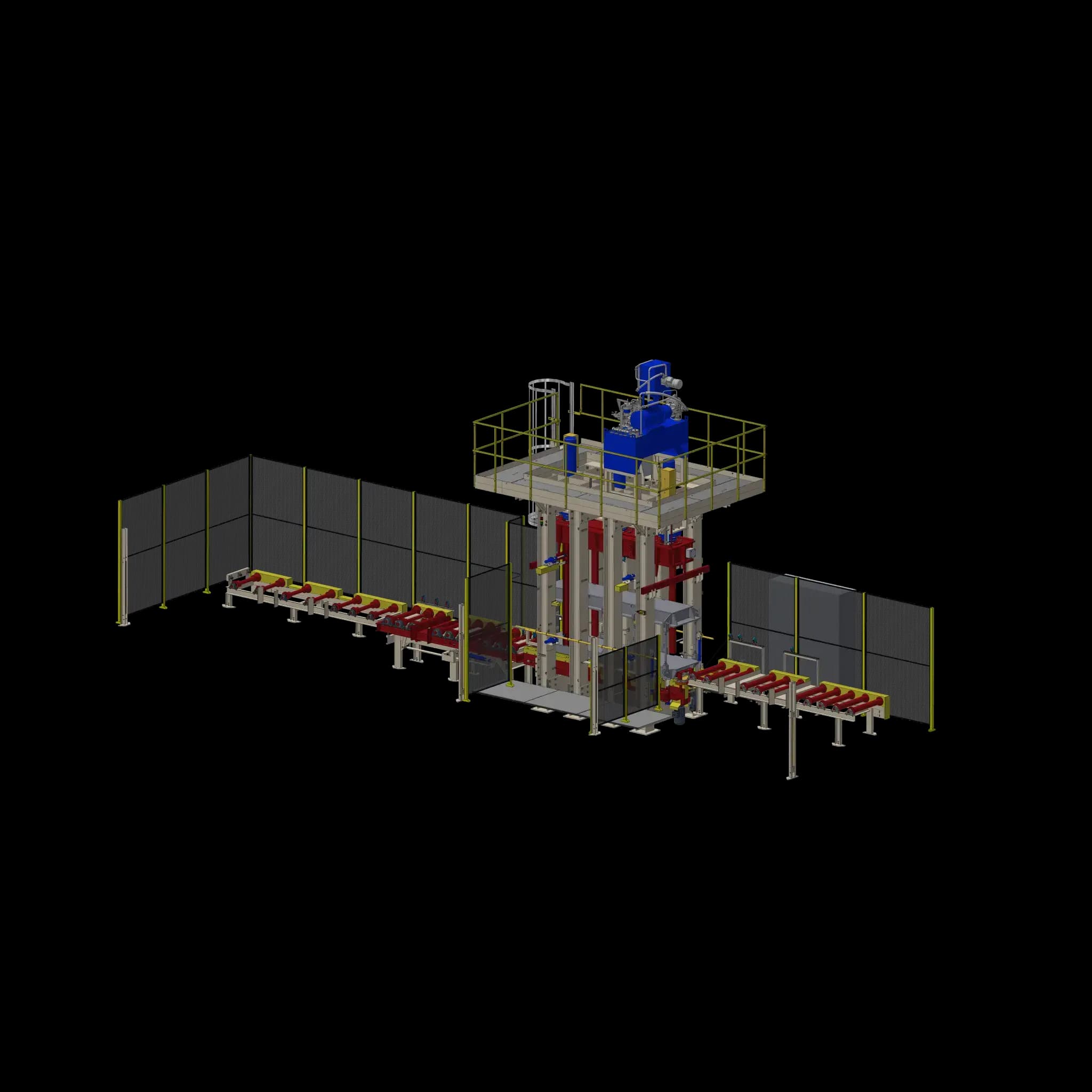
Key features of EltoBoards
-
fire rating: Euroclass B-s1,d0, optionally as non-combustible A2-s1,d0
-
density: 1100 kg / m³
-
standard thickness: 12-25 mm
-
acoustic performance: Rw~35-40
-
thermal conductivity (λ): 0.17 W/mK
-
accepts stucco, paint or veneer as finishing
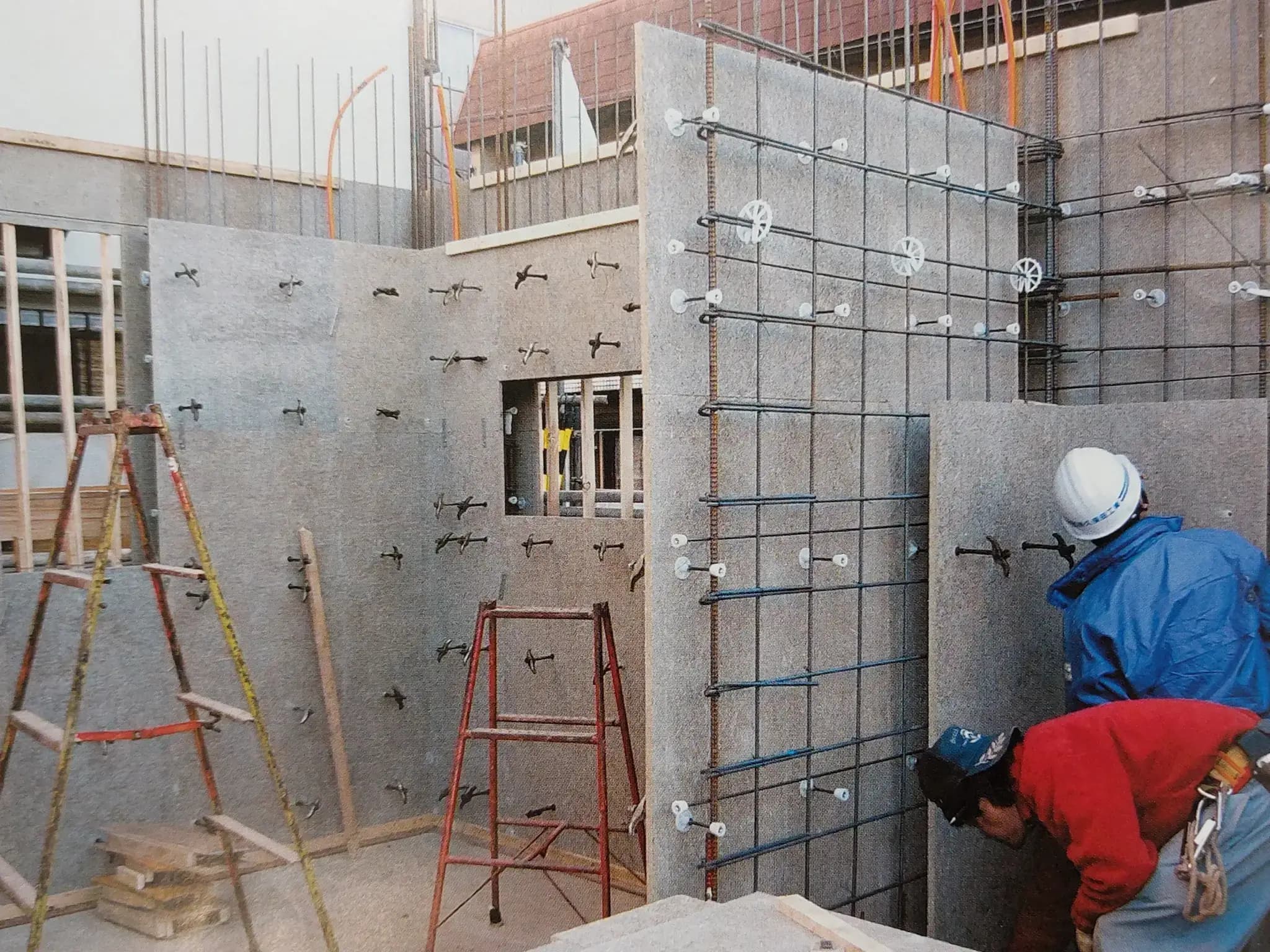
FAQ
How do these boards perform in terms of fire resistance?
WWCBs are inherently fire-resistant, achieving classifications such as B-s1,d0 and A2-s1,d0 (non-combustible) according to EN standards. The inclusion of mineral wool, EPS or XPS cores enhances this fire resistance, providing added safety in building constructions.
What are the electric power requirements to operate a WWCB plant?
For the Eltomation production line alone, the estimated installed capacity is approx. 900 kVA. When adding finishing operations, total installed power requirements are estimated at 1800 kVA.
How can you promote sustainable products if cement is used in the recipe?
While cement production contributes to CO₂ emissions, the industry is actively working on solutions to reduce its impact. In WWCB production, more than half of the board’s mass consists of renewable wood and water, making it a more sustainable option than many traditional building materials. Additionally, the low density of WWCB means that less material is needed to cover a given volume, further improving its environmental footprint. In general, we can state that 1 m³ of wood used creates approx. 4 m³ of end product.
Our plants are designed to (optionally) use LC3 cement as a lower-carbon alternative to standard Portland cement without compromising board quality. In addition, many of our clients add a percentage of limestone to reduce the overall cement content, further lowering emissions while maintaining durability and performance.
Do you also provide technical assistance in the ramp up phase?
Yes. Several Eltomation personnel will remain on site for 6 weeks after first commissioning to make sure the plant runs smoothly, and local operators / supervisors are properly trained.
Have other questions?
We would love to get in touch to discuss your needs.
Reach out to us today!