Mould Separating and Stacking
Mould Separating and Stacking
Main advantages
At Eltomation, we are constantly working to improve product quality, plant efficiency, and overall performance. One area of focus, based on discussions with our existing clients, is the Demoulding Operation. While the traditional demoulding method has served WWCB plants successfully for years, we are proud to introduce an advanced Demoulding and Empty Mould Handling System. This new system is designed for seamless integration into new WWCB plants but is also available as a modernization upgrade for existing production lines.
- Boards are fully supported when demoulded
- Much more controlled operation
- Much longer life-time of the moulds
- No more scratches on the board surface
- Less stoppages of the Forming Line
- Seamlessly exchange empty moulds
- Robotic operation ensures secure operation with reduced downtime
Steps in demoulding
- A newly designed Robotic Full Mould Destacking Unit takes the full mould from the top of a stack.
- A turner rotates the full mould by 180 degrees over its long axis, while fully supporting the fresh board.
- A newly designed Mould Board Separator separates the mould and board in a controlled manner.
- The released board is discharged to the pre-trimming and board stacking group.
- The empty mould is again turned by 180 degrees over its long axis and returns to the forming line.
- Empty forms coming from the demoulding operation go to the Robotic Empty Mould Stacker.
- The robot will create a small buffer of empty moulds to accommodate short line interruptions.
- The robot can build stacks of empty moulds, which can be taken out of the main line at the end of a shift.
- In the same process, new moulds can seamlessly be introduced to the line.
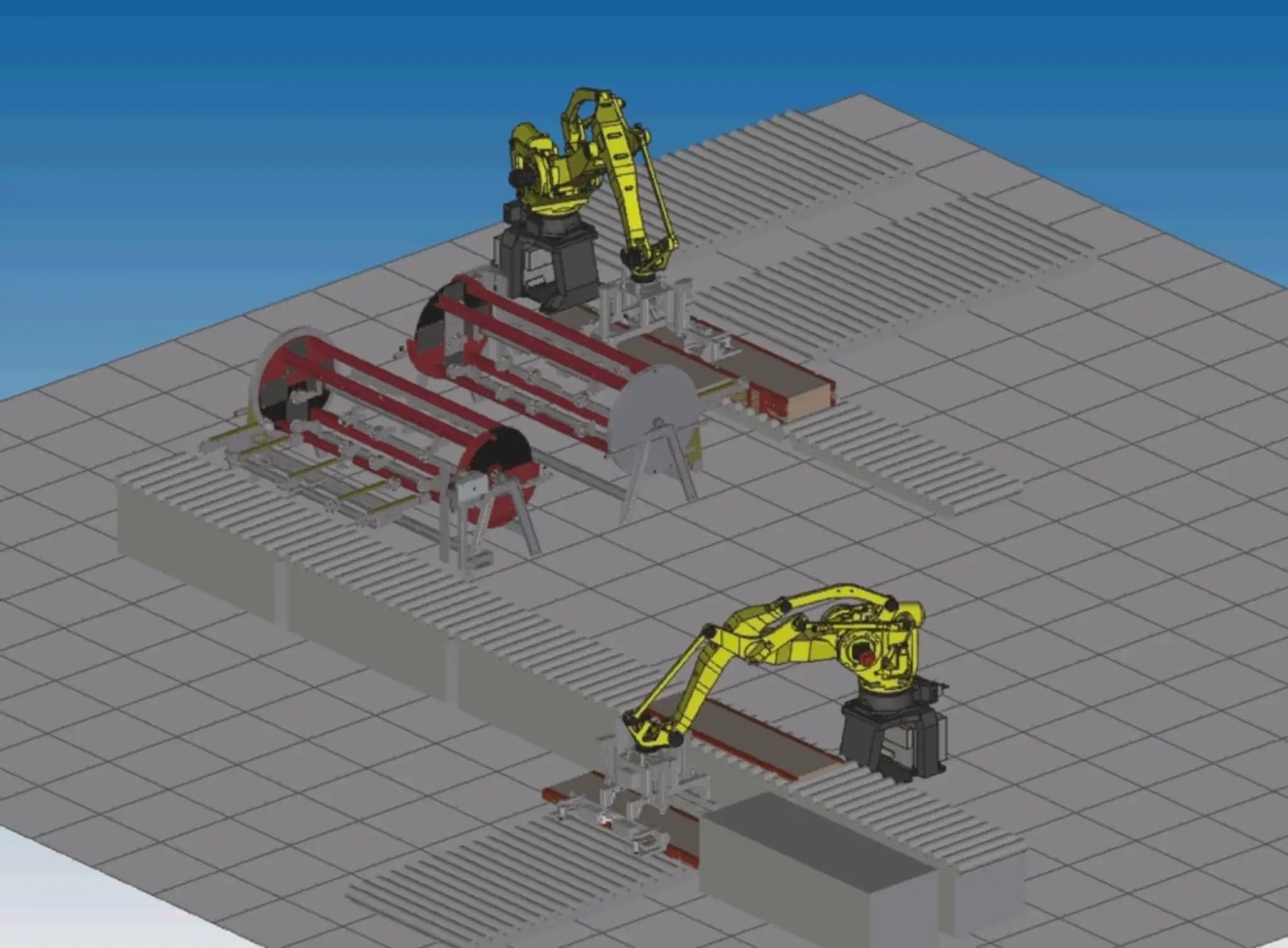